鋅合金壓鑄廠壓鑄件滲漏的處理方法
一、滲漏原因排查
(一)模具因素
模具的質(zhì)量與狀況對(duì)壓鑄件成型起著關(guān)鍵作用。模具設(shè)計(jì)不合理,如澆口位置不當(dāng)、排氣系統(tǒng)不完善,會(huì)導(dǎo)致金屬液填充不均勻,在壓鑄件內(nèi)部形成氣孔、縮孔,從而引發(fā)滲漏。模具表面磨損、有裂紋,會(huì)使壓鑄件表面不平整,存在微小縫隙,液體或氣體容易由此滲漏。檢查模具時(shí),需仔細(xì)查看澆口、排氣槽、分型面等部位,確認(rèn)是否存在上述問題。
(二)壓鑄工藝參數(shù)
壓鑄過程中的工藝參數(shù)設(shè)置不當(dāng),是造成壓鑄件滲漏的常見原因。壓鑄壓力不足,金屬液無法充分填充模具型腔,容易產(chǎn)生疏松、孔洞;壓鑄速度過快,會(huì)使金屬液在型腔中產(chǎn)生渦流,卷入大量氣體,形成氣孔;保壓時(shí)間過短,無法對(duì)壓鑄件進(jìn)行充分補(bǔ)縮,也會(huì)導(dǎo)致內(nèi)部出現(xiàn)縮孔。需要對(duì)壓鑄過程中的壓力、速度、時(shí)間等參數(shù)進(jìn)行詳細(xì)記錄和分析,判斷是否處于合理范圍。
(三)合金材料問題
鋅合金材料的質(zhì)量參差不齊,若材料中雜質(zhì)含量過高,或者成分比例不符合標(biāo)準(zhǔn),會(huì)影響合金的致密性和強(qiáng)度,增加滲漏風(fēng)險(xiǎn)。例如,鐵、鉛等雜質(zhì)含量過多,會(huì)降低鋅合金的流動(dòng)性和韌性,使壓鑄件更容易出現(xiàn)缺陷。對(duì)使用的鋅合金材料進(jìn)行成分檢測(cè),查看是否符合相關(guān)標(biāo)準(zhǔn)和生產(chǎn)要求。
(四)后續(xù)加工影響
壓鑄件在后續(xù)加工過程中,如機(jī)械加工、熱處理等,如果操作不當(dāng),也可能破壞壓鑄件的內(nèi)部結(jié)構(gòu),導(dǎo)致滲漏。例如,鉆孔時(shí)孔徑過大、過深,會(huì)損傷壓鑄件內(nèi)部的致密層;熱處理溫度過高或時(shí)間過長(zhǎng),會(huì)使壓鑄件內(nèi)部組織發(fā)生變化,產(chǎn)生裂紋。檢查后續(xù)加工工序,分析是否存在不當(dāng)操作。
二、針對(duì)性解決方案
(一)模具優(yōu)化與維護(hù)
根據(jù)檢查結(jié)果,對(duì)模具進(jìn)行優(yōu)化設(shè)計(jì)。調(diào)整澆口位置,確保金屬液能夠均勻填充型腔;改進(jìn)排氣系統(tǒng),增加排氣槽的數(shù)量和尺寸,提高排氣效率,減少氣體殘留。定期對(duì)模具進(jìn)行維護(hù)保養(yǎng),及時(shí)修復(fù)磨損和裂紋部位,保證模具表面的光潔度和精度。例如,采用電火花加工、激光熔覆等技術(shù)對(duì)模具進(jìn)行修復(fù)。
(二)工藝參數(shù)調(diào)整
通過試驗(yàn)和數(shù)據(jù)分析,確定合理的壓鑄工藝參數(shù)。適當(dāng)提高壓鑄壓力,一般可在原有壓力基礎(chǔ)上增加10%-20%,以保證金屬液充分填充型腔;調(diào)整壓鑄速度,根據(jù)壓鑄件的復(fù)雜程度和尺寸大小,選擇合適的低速填充和高速填充階段;延長(zhǎng)保壓時(shí)間,確保對(duì)壓鑄件進(jìn)行充分補(bǔ)縮,保壓時(shí)間可延長(zhǎng)10-30秒。在調(diào)整參數(shù)后,進(jìn)行小批量試生產(chǎn),檢測(cè)壓鑄件的質(zhì)量,根據(jù)結(jié)果進(jìn)一步優(yōu)化參數(shù)。
(三)材料質(zhì)量把控
選擇質(zhì)量可靠的鋅合金材料供應(yīng)商,嚴(yán)格把控材料的進(jìn)貨檢驗(yàn)環(huán)節(jié)。對(duì)每批次的鋅合金材料進(jìn)行成分分析和性能測(cè)試,確保材料符合生產(chǎn)要求。建立材料質(zhì)量追溯體系,一旦發(fā)現(xiàn)材料問題,能夠及時(shí)追溯到供應(yīng)商,采取相應(yīng)的處理措施。
(四)規(guī)范后續(xù)加工
制定嚴(yán)格的后續(xù)加工工藝標(biāo)準(zhǔn)和操作規(guī)程,對(duì)操作人員進(jìn)行培訓(xùn),確保其按照標(biāo)準(zhǔn)進(jìn)行操作。在機(jī)械加工過程中,合理控制加工參數(shù),避免損傷壓鑄件的內(nèi)部結(jié)構(gòu);在熱處理過程中,嚴(yán)格控制溫度和時(shí)間,采用合適的熱處理工藝,如退火、回火等,提高壓鑄件的性能。
三、預(yù)防措施
(一)質(zhì)量檢測(cè)體系完善
建立完善的質(zhì)量檢測(cè)體系,在壓鑄生產(chǎn)的各個(gè)環(huán)節(jié)設(shè)置檢測(cè)點(diǎn)。采用先進(jìn)的檢測(cè)設(shè)備,如X光探傷儀、超聲波探傷儀等,對(duì)壓鑄件進(jìn)行內(nèi)部缺陷檢測(cè);使用氣密檢測(cè)儀對(duì)壓鑄件進(jìn)行密封性檢測(cè),及時(shí)發(fā)現(xiàn)潛在的滲漏問題。對(duì)檢測(cè)數(shù)據(jù)進(jìn)行統(tǒng)計(jì)分析,找出質(zhì)量問題的規(guī)律和原因,采取針對(duì)性的改進(jìn)措施。
(二)員工培訓(xùn)與管理
加強(qiáng)員工的技能培訓(xùn),提高員工對(duì)壓鑄工藝、模具維護(hù)、質(zhì)量檢測(cè)等方面的專業(yè)知識(shí)和操作技能。定期組織員工進(jìn)行質(zhì)量意識(shí)培訓(xùn),讓員工認(rèn)識(shí)到產(chǎn)品質(zhì)量的重要性,樹立全員參與質(zhì)量控制的理念。建立健全員工績(jī)效考核制度,將產(chǎn)品質(zhì)量與員工的績(jī)效掛鉤,激勵(lì)員工提高工作質(zhì)量。
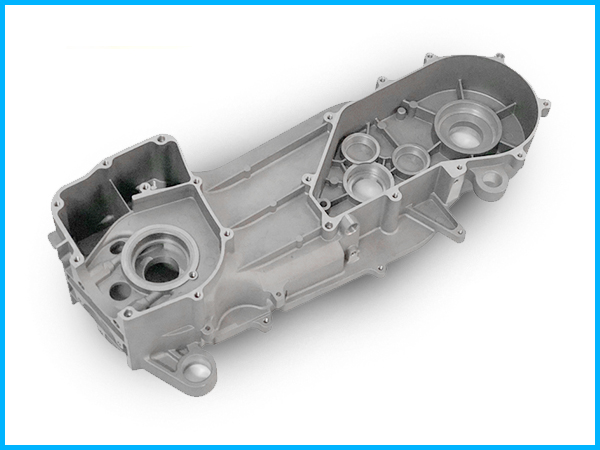